The use of 3D printing technologies in medical technology has increased significantly in recent years, with silicone 3D printing being a particularly promising development. This technology enables the production of customised implants and prostheses that set new standards in both functionality and biocompatibility. In this article, we will explore the advantages, challenges and application examples of silicone 3D printing in medical technology.
Why silicone?
Silicone is a material of choice in medical technology due to its unique properties. It is biocompatible, flexible, temperature-resistant and has a high chemical stability. These properties make it ideal for medical applications where the material comes into direct contact with the human body. Traditionally, silicone implants and prostheses have been manufactured using casting processes, but 3D printing is opening up completely new possibilities here.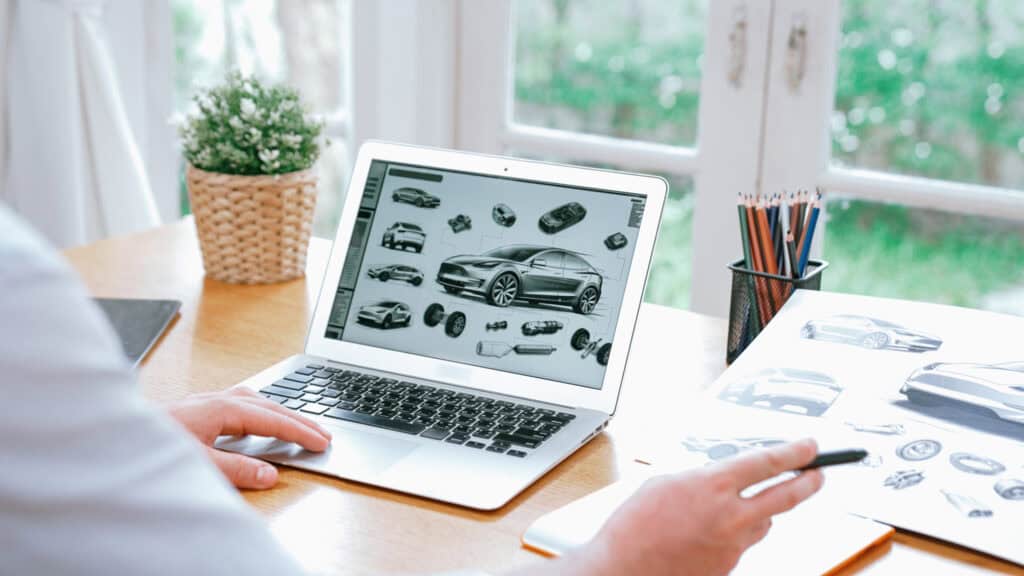
Advantages of silicone 3D printing
- Personalisation: One of the biggest advantages of silicone 3D printing is the possibility of customisation. Each implant or prosthesis can be precisely adapted to the anatomical conditions of the patient. This not only results in a better fit, but also in greater functionality and improved comfort for the wearer.
- Speed and efficiency: Compared to traditional manufacturing processes, silicone 3D printing can significantly speed up the production process. Since no elaborate moulds or tools are needed, implants and prostheses can be produced in less time and at lower cost.
- Complex geometries: 3D printing enables the production of complex, organic structures that would be difficult or impossible to achieve using traditional methods. This is particularly important for applications in which an implant or prosthesis must be perfectly integrated into the surrounding tissue.
- Material efficiency: Since 3D printing only uses the amount of silicone actually needed for the component, material waste is significantly reduced. This not only helps to reduce costs, but is also more environmentally friendly.
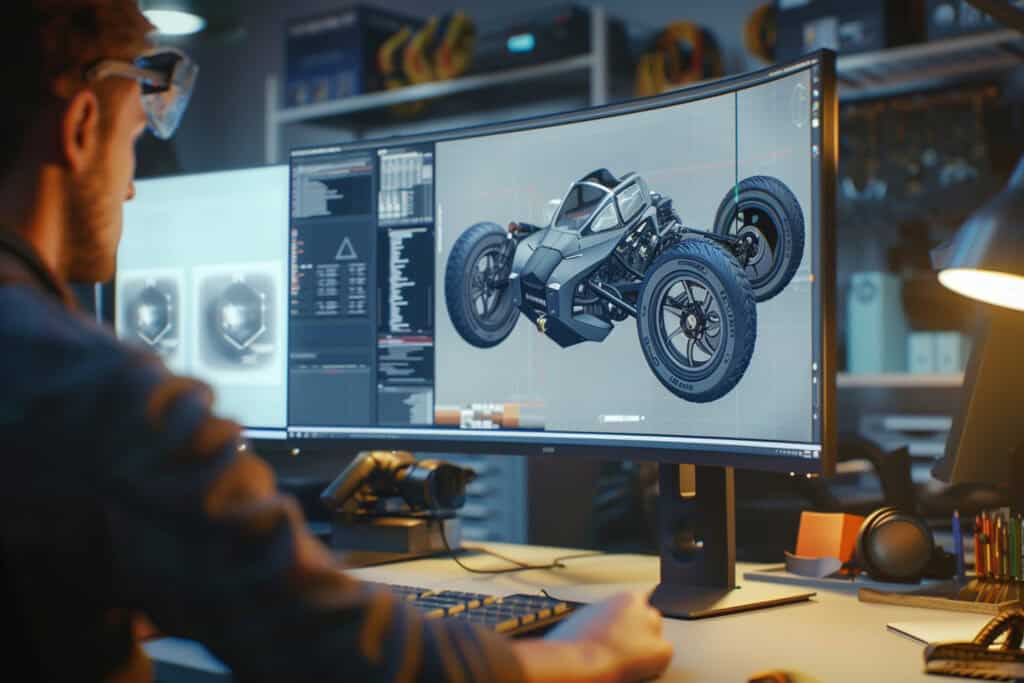
Examples of applications in medical technology
- Hearing aids: silicone 3D printing is used to create customised earpieces for hearing aids. These must be precisely tailored to the patient’s ear canal to ensure comfort and optimal sound transmission. 3D printing enables an exact replica of the ear canal based on digital scans, ensuring a perfect fit and maximising the efficiency of the hearing aid. 2. Heart valves and vascular models: silicone 3D printing is also used to create models for surgical planning and training, particularly for complex heart surgeries. Printed silicone models of heart valves and blood vessels allow surgeons to study the patient’s anatomy in detail and plan the operation in advance. In some cases, functional prototypes of heart valves have even been printed in silicone to test future implantation methods. 3. Voice prostheses: For patients who have lost their voice due to a laryngectomy, voice prostheses made of silicone can be life-changing. These prostheses are often customised to simulate the function of the vocal cords and enable the most natural vocal production possible. Silicone 3D printing plays a key role in the production of these highly specialised devices. 4. Tracheal Stents: Silicone stents are used to keep the windpipe open, for example in patients with tracheal stenosis (narrowing of the windpipe). Traditionally, these stents were made in standard sizes, which were not always optimal for every patient. 3D printing can be used to create customised stents that are precisely tailored to the patient’s anatomy, significantly improving efficacy and comfort. 5. Patient-specific surgical instruments: In some cases, silicone 3D printing is used to create customised surgical instruments that are specifically designed to meet the needs of the patient and the requirements of the operation. These instruments can be used, for example, in minimally invasive surgery or in the treatment of complex fractures where standard instruments are insufficient. 6. Prosthetics (facial prostheses): In addition to the nose and ear prostheses already mentioned, other facial parts, such as eyelids or cheekbones, are also produced using silicone 3D printing. These prostheses are often used in patients who have suffered accidents, cancer or congenital defects. 3D printing enables an exact fit to the existing facial structures, resulting in a natural appearance and high level of acceptance. 7. Soft tissue reconstruction: In plastic and reconstructive surgery, silicone 3D printing is increasingly being used to manufacture implants for the reconstruction of soft tissue, e.g. after tumour resections. These implants are individually customised to the defect size and shape of the patient, which leads to better aesthetic and functional results.
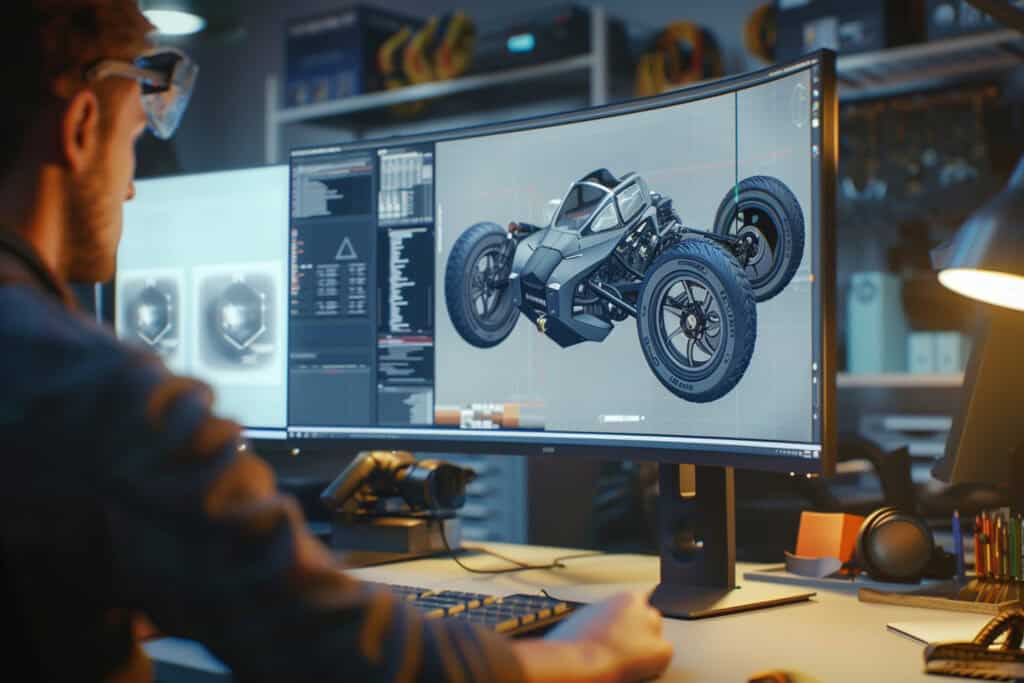
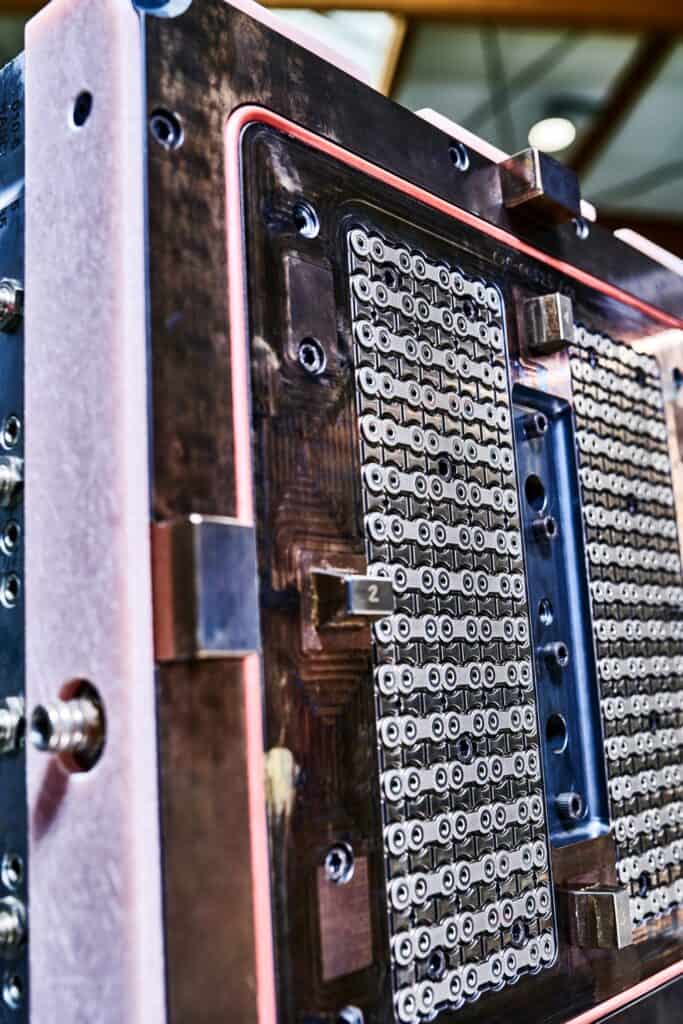
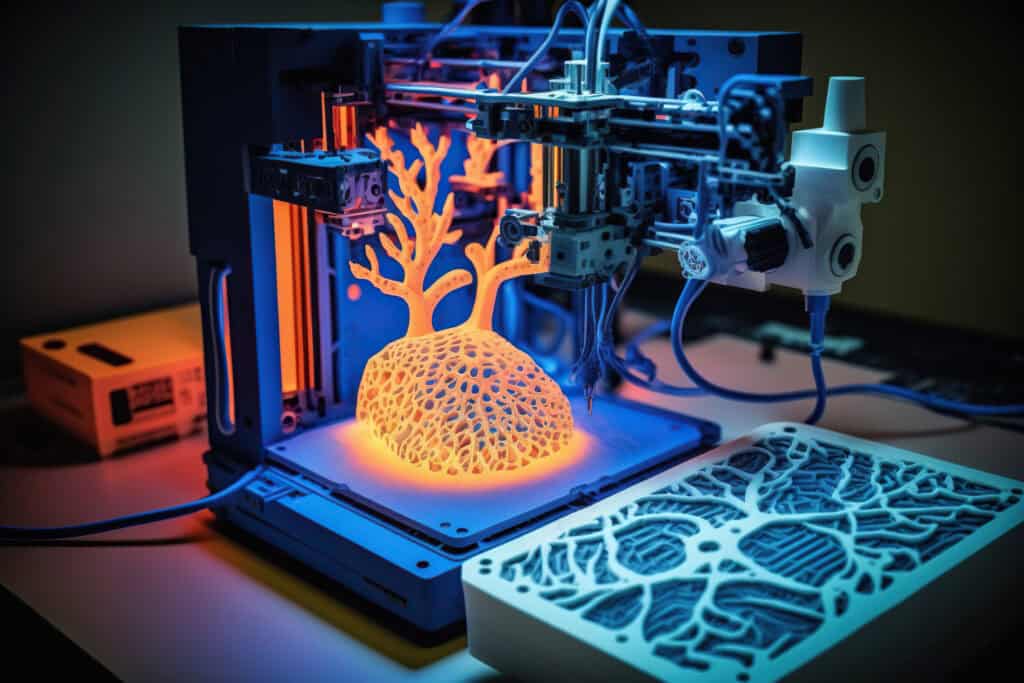